- Printer Model
- Voron 2.4
- Extruder Type
- Clockwork 2
- Cooling Type
- Stealthburner
Hi All,
Happy New Year!
I thought I would throw this one out there before diving too much further down the rabbit hole.
With ABS on my new build (2.4 350mm) I am having some challenges on large flat panels and am wondering where I should start tinkering to try to fix them. I have run through the Ellis guide for bed squish, bed adhesion, extrusion multiplier etc so the printer is actually running quiet well for smaller pieces.
Printing wise I have a challenging environment: Loft, currently 10deg celcius, good airflow (good for fumes, not for heating). Chamber is getting up to 40c max (measured with a separate device inside/top so accurate).
While printing a couple of items to help with the chamber temps [bed fan holders] I noticed it is working well on bed adhesion with all items but the external blanking plate for the top vent in the 2.4 has some artifacts on the top surface - it looks like the top layers were pulling away from the infill. Looking at possible root cause to try to prevent while it is cold (London UK so some months to go). 2.4 is fully enclosed and I have a blanket over it but no option to heat the loft and no option to put it elsewhere so looking at thoughts in this environment.
Printing specs:
Polymaker Polylite ABS in gray
260 hotend
105 bed (actual reads around 95 with an ir gun)
0.95 extrusion multiplier
max volumetric speed set to 10mm3/s (SB E3D Voron 60W/HF brass 0.4mm)
speeds and accel on a conservative end using superslicer.
My guess was this occurred on the largest piece so it was getting up to speed on the longer runs and dumping too much heat with a poor chamber temp but some of you ABS champs may have a good idea at where exactly to look and how to mitigate this issue until I can get chamber temps a little higher i.e have to print stuff to fix stuff
. Other then this issue on the largest item I am quite please with the print quality.
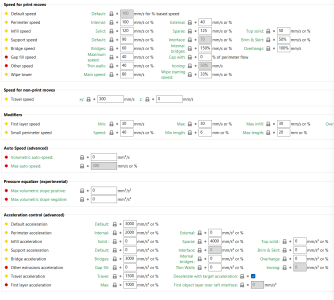
Happy New Year!
I thought I would throw this one out there before diving too much further down the rabbit hole.
With ABS on my new build (2.4 350mm) I am having some challenges on large flat panels and am wondering where I should start tinkering to try to fix them. I have run through the Ellis guide for bed squish, bed adhesion, extrusion multiplier etc so the printer is actually running quiet well for smaller pieces.
Printing wise I have a challenging environment: Loft, currently 10deg celcius, good airflow (good for fumes, not for heating). Chamber is getting up to 40c max (measured with a separate device inside/top so accurate).
While printing a couple of items to help with the chamber temps [bed fan holders] I noticed it is working well on bed adhesion with all items but the external blanking plate for the top vent in the 2.4 has some artifacts on the top surface - it looks like the top layers were pulling away from the infill. Looking at possible root cause to try to prevent while it is cold (London UK so some months to go). 2.4 is fully enclosed and I have a blanket over it but no option to heat the loft and no option to put it elsewhere so looking at thoughts in this environment.
Printing specs:
Polymaker Polylite ABS in gray
260 hotend
105 bed (actual reads around 95 with an ir gun)
0.95 extrusion multiplier
max volumetric speed set to 10mm3/s (SB E3D Voron 60W/HF brass 0.4mm)
speeds and accel on a conservative end using superslicer.
My guess was this occurred on the largest piece so it was getting up to speed on the longer runs and dumping too much heat with a poor chamber temp but some of you ABS champs may have a good idea at where exactly to look and how to mitigate this issue until I can get chamber temps a little higher i.e have to print stuff to fix stuff

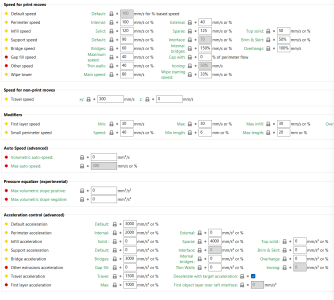