billgeek
Member
I'm not certain if this is hardware, firmware or slicer related, but I've been running my Trident for about six months now. I thought the print quality is pretty decent, but I've since purchased a Bambu Lab P1S and this made me realize what "round" actually means.
Circular objects on the Trident tend to come out as "segmented" lines.
I followed and dialed in my printer using the excellent guide by Ellis for tuning the machine and am using BambuStudio to slice my model.
I've tried this with "Arc fitting" enabled or disabled on the Trident, but the result remains the same. (I needed to add "gcode_arcs" to the config file on my Trident and set the resolution to 0.25mm - any lower and I get "timing" issues)
This first picture is from the Trident. Notice the "wobble" on the lower half below the knurled grip. I took this picture in the worst possible light to exaggerate the issue:
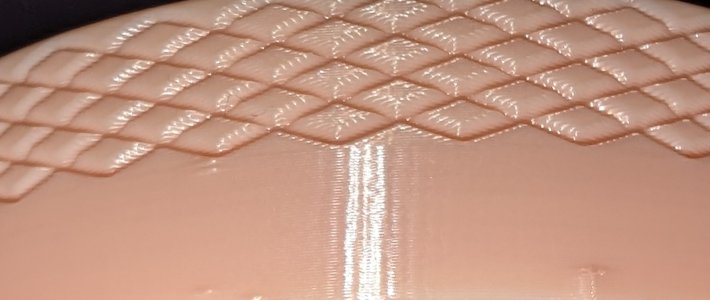
This next picture is from the P1S. Aside from a few lines appearing slightly darker, the walls on the lower half are perfectly circular. (This picture was also taken in the worst possible lighting conditions)
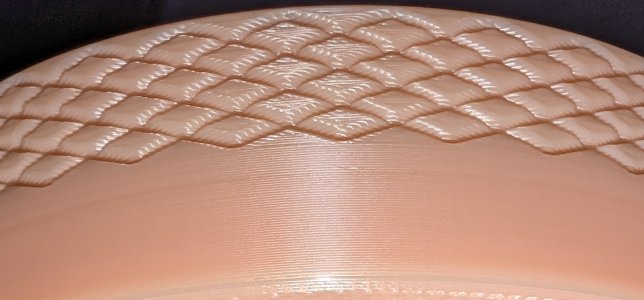
I also own the Creality K1 and it looks the absolute worst, with the lines creating a texture on the cylinder:
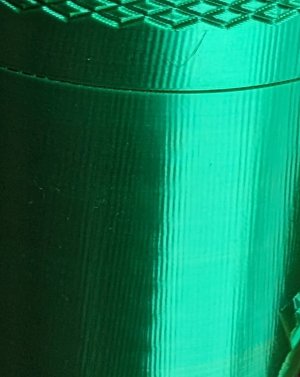
So I guess the question is: What could be the cause of this, and how can I go about addressing the issue? I fully realize that the Bambu is a proprietary machine and all that, but at the end of the day it's "just another" CoreXY machine.
Circular objects on the Trident tend to come out as "segmented" lines.
I followed and dialed in my printer using the excellent guide by Ellis for tuning the machine and am using BambuStudio to slice my model.
I've tried this with "Arc fitting" enabled or disabled on the Trident, but the result remains the same. (I needed to add "gcode_arcs" to the config file on my Trident and set the resolution to 0.25mm - any lower and I get "timing" issues)
This first picture is from the Trident. Notice the "wobble" on the lower half below the knurled grip. I took this picture in the worst possible light to exaggerate the issue:
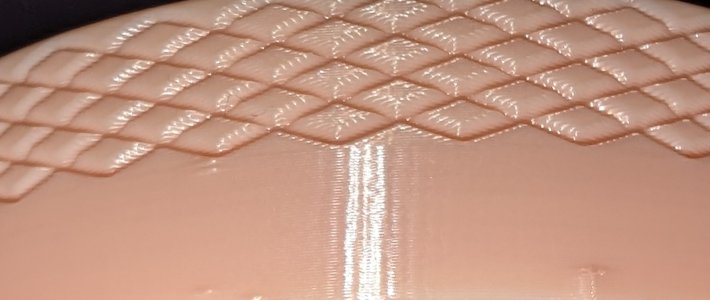
This next picture is from the P1S. Aside from a few lines appearing slightly darker, the walls on the lower half are perfectly circular. (This picture was also taken in the worst possible lighting conditions)
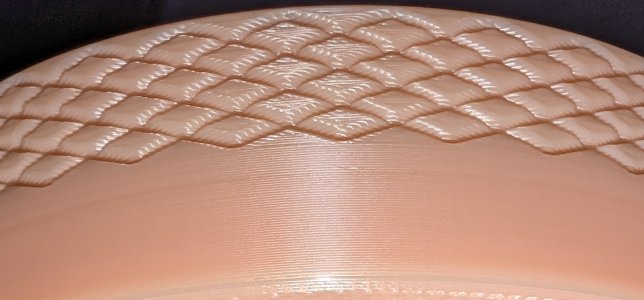
I also own the Creality K1 and it looks the absolute worst, with the lines creating a texture on the cylinder:
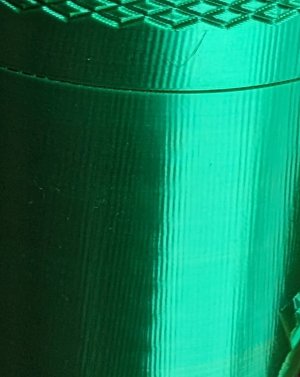
So I guess the question is: What could be the cause of this, and how can I go about addressing the issue? I fully realize that the Bambu is a proprietary machine and all that, but at the end of the day it's "just another" CoreXY machine.