- Printer Model
- EnderWire IDEX
- Extruder Type
- Galileo
- Cooling Type
- Stealthburner
I've been feeling (overly?) ambitious and I decided that instead of the relatively easy task of converting my E3 Pro to a Switchwire using boubounokefalos resources, I'd complicate things by making an IDEX Enderwire. Why? I've got a Raise 3D E2 that is IDEX and being able to print with dual materials or having disolvable supports has been a game changer. The problem with the E2 is it's sllllloooooowwwww and IdeaMaker, while a good slicer, doesn't get nearly as much love as Prusa Slicer or Cura. So I thought "Lets do this!" That being said, all the printed parts will be done on the E2 in ASA.
Anyway, I've been researching the EW IDEX conversion for awhile and I've come across a couple helpful git's (ankurv2k6's and cabhinlab's) that where enough to get me started, but neither git has been updated in over 2 years. The Cabinlab blog did help with one key problem, kenematics for an EW IDEX.
Design Goals:
Anyway, I've been researching the EW IDEX conversion for awhile and I've come across a couple helpful git's (ankurv2k6's and cabhinlab's) that where enough to get me started, but neither git has been updated in over 2 years. The Cabinlab blog did help with one key problem, kenematics for an EW IDEX.
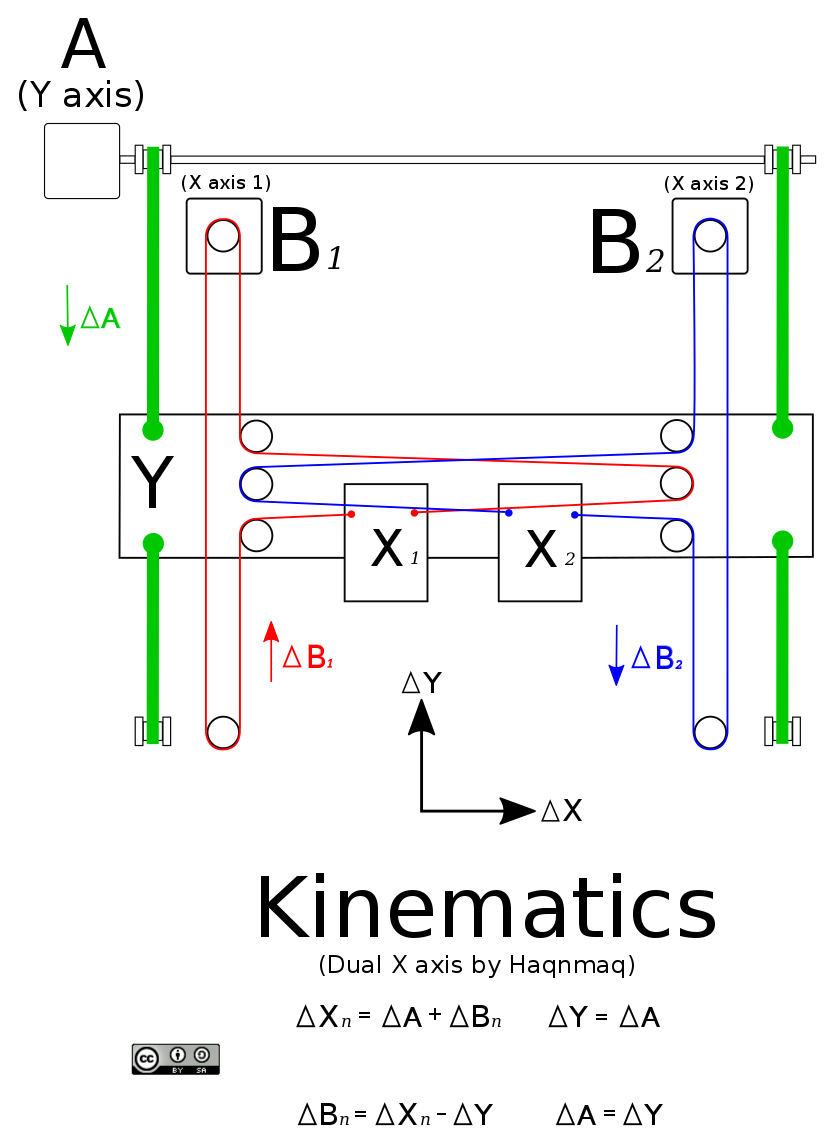
Design Goals:
- Use as many parts from my E3 Pro as possible
- Core XZ'ish
- Stealthburners with Gallaleo 2 extruders, hotends are TBD
- CANBUS on both extruders
- I want to experiment with Nylon's and glass and CF blends, so fully enclosable and maybe active heating?
- Nevermore or some other air circulation system (possibly integrate a heater into this?)
- Widened printer by 110mm to 440mm
- Remixed the Z-axis motor mounts (botom motors) so that they clamp on the inside of the frame instead of the outside. This allows for smooth outter pannels with fewer protrusions.
- For the X gantry I'm going to use a 350mm rail along with a 350mm extrusion.
- Still need to remix the XZ blocks for IDEX, these will probably be unique for each side.
- Remixed the Stealthburner brackets so that the belt channels are wider on one side than the other to allow for minimial interfearance with the belt as the other extruder moves.
- The eagle eyed may have noticed that I removed the belt tensioner off the Z motor mounts. With the new mounting location, tensioning the belts would have been a PITA. Instead, I took inspiration from my V0.1 and designed a tensioner mechanisim around the x-axis motors. They are mostly the same from one side to the other but I did integrate the counterweight pulley into the left motor mount (not shown).
- The big milled 40 x 40 extrusion that the y-axis rests on will be reused. I think the plan for that is going to be getting another 40 x 40 extrusion and cutting it down to size and then printing some parts to stitch it together into one piece. Alternatively, I can print one big piece and use an M5x100mm bolt to hold everything together. This will take a bit more thought.
- Pannels, I need to remix the pannels, covers, extensions and grills. though they are low priority.
- Electronics. I doubt the stock E3 Pro power supply can handle double the motors and extruders, so I'll gonna to have to source a more robust one. For the MCU, I'm thinking about the BTT Octopus, and I'll likely use a Raspberry Pi 4b and a 5VDC buck converter to power it.