3dCase
Well-known member
So the journey is done and the rebuilding has started.
The plan is to build it up as it came apart, then troubleshoot. The reason is that I never worked with this printer before, and my dad only very little. I do not know the original builder, so no knowledge of how well this person did the work.
I will simply stick it together and let it find its own squareness and see what we have.
Also this is my first klipper machine so that part will be challenging also.
First day of the build was the unpacking and evaluating if there had been any bumps or knocks. All seems fine so I can start.
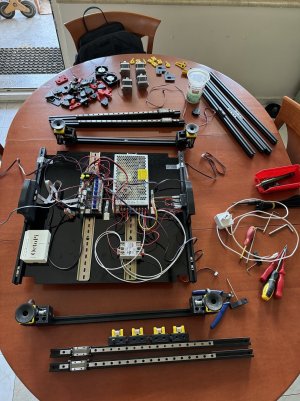
I placed the parts on the kitchen table, because my work table is full with other unfinished projects such as my own design printer, A 3d printed working Harley Davidson model I drew up in cad, and several other half forgotten things.
This way you can sort your parts and any amount of hardware quickly shows you where they are supposed to go. I used to rebuild printing machines in the field for years and always as the machine was placed out in parts over several pallets on the work floor, the owner came by to ask if I would manage to get that all back together again. The answer till now was always a resounding yes, so I am not going to change that any day soon.
Next I stuck the base together, obviously first go with the right member on the left, just as a test
Once that was out of the way it all slipped in nicely.
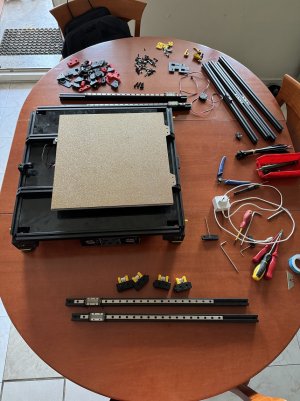
At this point I am already thinking ahead and trying to spot my next mistake. So far so good I think and I proceed with the uprights.
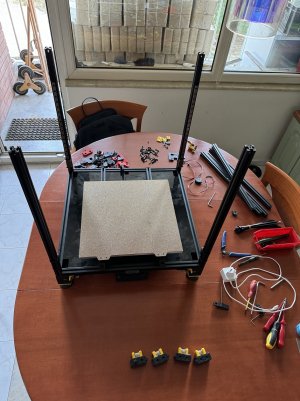
I have not yet fixed the z motor brackets yet, as I am not yet sure if it will be possible to thread the belts through with the motor tight. I think it will but I am expecting it to be easier this way.
Now I fit the top members.
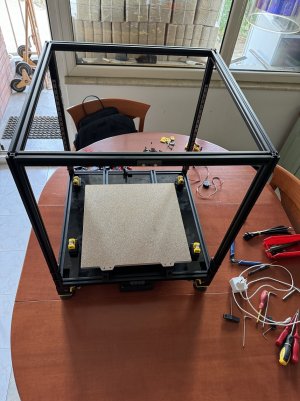
I forgot to register exactly where those tensioners went so I had to think that through a bit harder, I think I know where they should go so the top members are in the right place and in the correct orientation.
Now we slip in the gantry
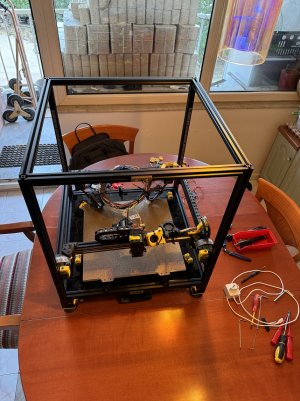
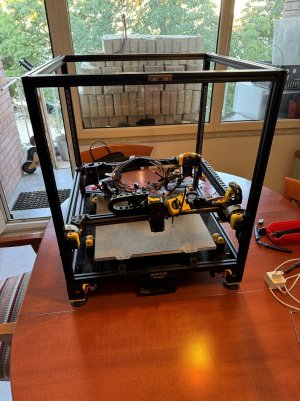
And instantly it looks more like a Voron already.
Now I fitted the carriage block screws to all four corners so the whole gantry can move up and down as it should.
I have to tie up the gantry and suspend it so I can pre-adjust a rough level.
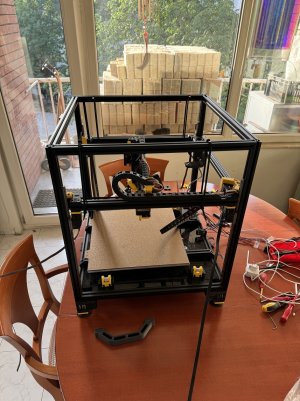
By adjusting those tie-wraps the gantry can be set to a reasonably accurate horizontal.
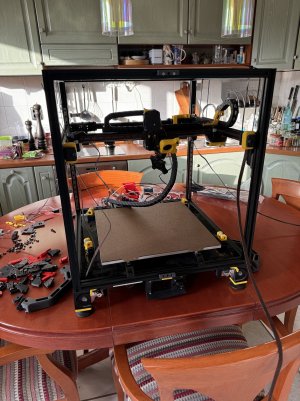
And that is where I am at right now. I will clean up that wiring a little and install some stretchy cable protecting sleeves in those cable chains. At the same time I will also thread the two rear z motor cables back in the cable chain. My dad had a problem and my brother found there were broken cables there so the two rear cables have been spliced and lived outside the cable chain.
Next installment soon!
Already enjoying the Voron feeling
The plan is to build it up as it came apart, then troubleshoot. The reason is that I never worked with this printer before, and my dad only very little. I do not know the original builder, so no knowledge of how well this person did the work.
I will simply stick it together and let it find its own squareness and see what we have.
Also this is my first klipper machine so that part will be challenging also.
First day of the build was the unpacking and evaluating if there had been any bumps or knocks. All seems fine so I can start.
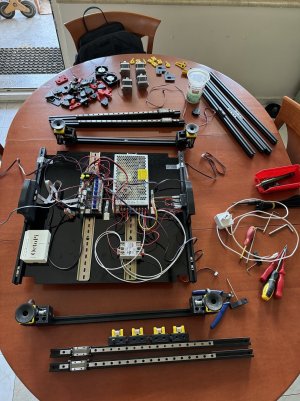
I placed the parts on the kitchen table, because my work table is full with other unfinished projects such as my own design printer, A 3d printed working Harley Davidson model I drew up in cad, and several other half forgotten things.
This way you can sort your parts and any amount of hardware quickly shows you where they are supposed to go. I used to rebuild printing machines in the field for years and always as the machine was placed out in parts over several pallets on the work floor, the owner came by to ask if I would manage to get that all back together again. The answer till now was always a resounding yes, so I am not going to change that any day soon.
Next I stuck the base together, obviously first go with the right member on the left, just as a test

Once that was out of the way it all slipped in nicely.
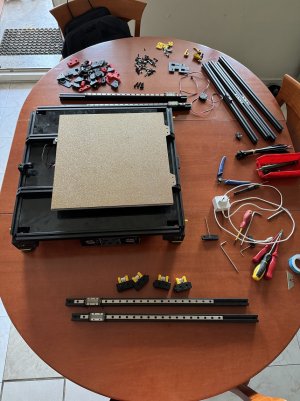
At this point I am already thinking ahead and trying to spot my next mistake. So far so good I think and I proceed with the uprights.
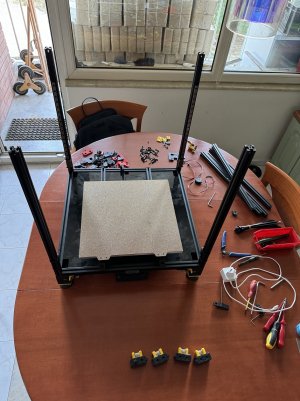
I have not yet fixed the z motor brackets yet, as I am not yet sure if it will be possible to thread the belts through with the motor tight. I think it will but I am expecting it to be easier this way.
Now I fit the top members.
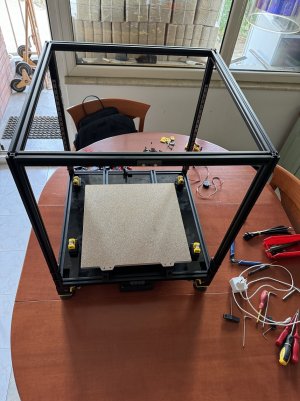
I forgot to register exactly where those tensioners went so I had to think that through a bit harder, I think I know where they should go so the top members are in the right place and in the correct orientation.
Now we slip in the gantry
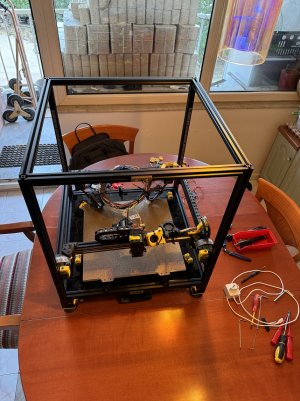
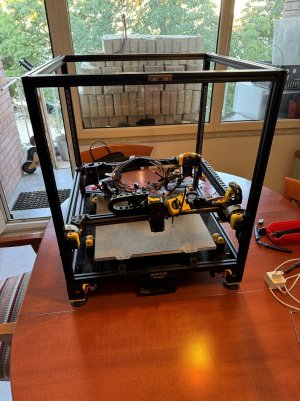
And instantly it looks more like a Voron already.
Now I fitted the carriage block screws to all four corners so the whole gantry can move up and down as it should.
I have to tie up the gantry and suspend it so I can pre-adjust a rough level.
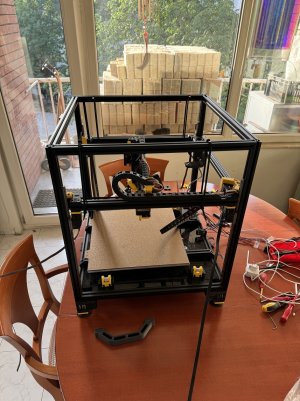
By adjusting those tie-wraps the gantry can be set to a reasonably accurate horizontal.
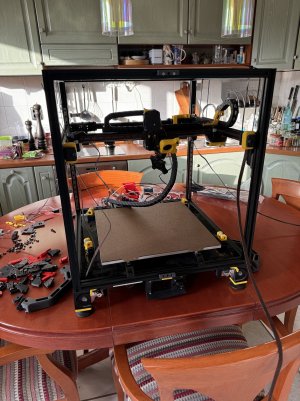
And that is where I am at right now. I will clean up that wiring a little and install some stretchy cable protecting sleeves in those cable chains. At the same time I will also thread the two rear z motor cables back in the cable chain. My dad had a problem and my brother found there were broken cables there so the two rear cables have been spliced and lived outside the cable chain.
Next installment soon!
Already enjoying the Voron feeling
