- Printer Model
- Trident
- Extruder Type
- Clockwork 2
- Cooling Type
- Stealthburner
Hi all - looking for some suggestions on what might be causing a couple of print quality issues I'm seeing on a fresh Trident build...
This printer is my second Voron printer. The first was a V2.4 which I completed a few months ago and that printer has been running great from day one. This printer (the Trident) is a rebuild of my original Hypercube printer that I built years ago following Tech2C's original plans. I've reused a lot of the extrusions. The build surface is also from the original (so it is 1/4" plate vs the 3/8" recommended for the Voron). I've reused two of the Z stepper/leadscrews with a 3rd purchased new for this build. A/B steppers are repurposed from the Hypercube as is the E3D V6 clone hotend. Electronics are all new for this build, with most of the stepper wires reused. I'm running a BTT Octopus v1.1 controller with an EBB SB2209 CAN controller at the StealthBurner. Also using ChaoticLabs aluminum TAP for the Z-Probe... here is a pic of the printer for context:
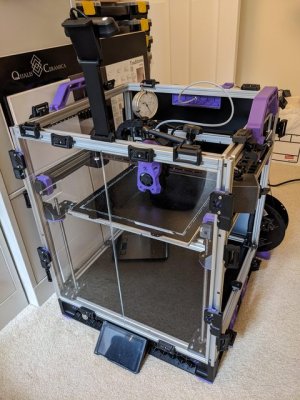
As far as I can tell everything is working well, except for two issues. First, I'm having surprisingly poor first layers. And second, I'm getting a weird effect on the corner of the FilamentCard test print.
So, the first layer problem... After adjusting my Z probe offset (remember, this is a TAP setup) if I try to print my first layer at anything less than 0.3mm layer height I get tearing of the first layer. But at 0.3mm layer height and above I get a very "wobbly" layer. It's almost as if the nozzle is moving up and down as it traverses. Some pics:
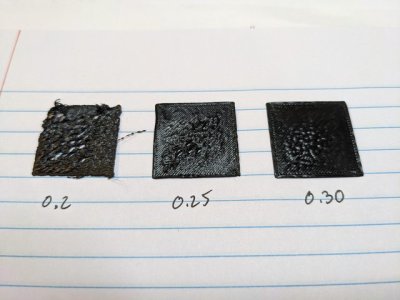
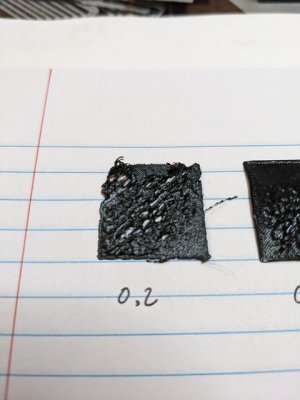
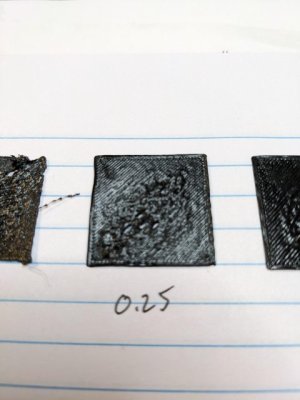
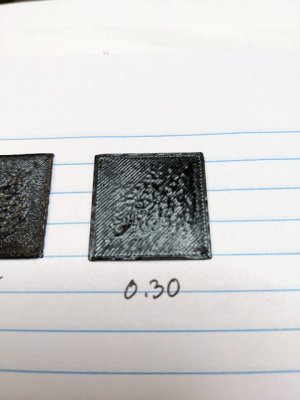
Obviously .2mm and .25mm layer heights are not sticking and the plastic (btw, this is Hatchbox PLA) is lifting/tearing away from the build surface. At .3mm I still seem to be getting some lifting that I assume is causing the waviness you can see in the last image, but it is not being torn away by the nozzle. I'm finding that even at .3mm layer height the lifting/tearing is hit-or-miss.
This is a shot of the edge of the (one layer thick) print. Trying to capture/show the waviness that I seem to be getting.
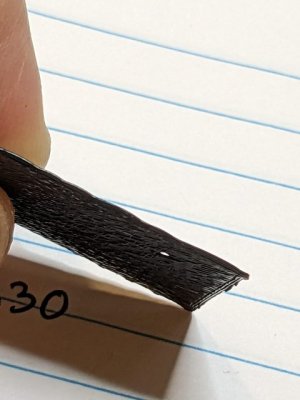
My V2.4 also is using TAP, but I'm using the printed version not the CL version, so I was thinking maybe that was part of the issue? At one point I was wondering if maybe I forgot to add the magnet which holds the print head down when not probing - checked that, the magnet is there. Since it looks to me like the nozzle might be moving up/down while printing I did a test where I homed the Z against a scale, then adjusted Z height down (bringing the build plate up) .005mm at a time recording the nozzle pressure against the scale at each step. If useful I can provide the data, but basically the pressure increased about 10g per .005mm step until it reached about 500g and the Z-probe triggered. After that the pressure remained at about 480g as the nozzle continued "down". That seemed to me like it was working as expected and it would take approx 500g downward force before the print head begins moving upwards, so not likely that the pressure from the filament pushing out the nozzle is causing the head to lift...
I also used a dial indicator in a similar test to see whether the head was actually moving as the bed was brought up in the same .005mm increments. I saw similar results on the scale and the stealthburner head was not lifting until I got close to 500g downward pressure and the TAP broke loose.
Second issue I'm seeing (maybe related?) - when I print the FilamentCard test print I'm getting a strange 'lifting' of the back-right corner:
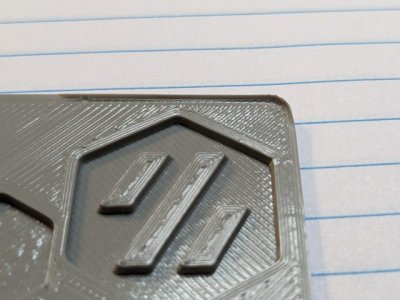
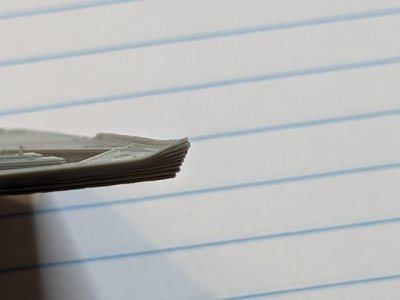
This is consistent across two spools of filament and I've not seen similar artifacts on other test prints:
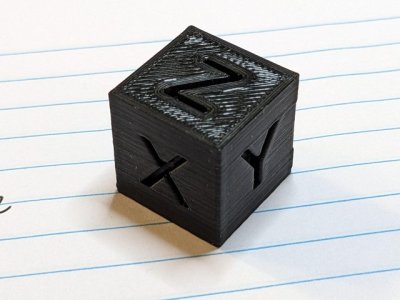
Leading me to assume it has something to do with the way the test card is beveled on that back edge.
BTW, this is the bottom of the test cube:
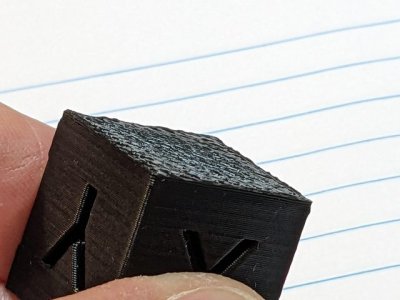
Note how it's wavy and uneven for the first few layers, then seems to settle down and print smoothly for the remaining layers.
I'm out of ideas on what to try for these problems. Any suggestions would be appreciated.
Thanks in advance!
This printer is my second Voron printer. The first was a V2.4 which I completed a few months ago and that printer has been running great from day one. This printer (the Trident) is a rebuild of my original Hypercube printer that I built years ago following Tech2C's original plans. I've reused a lot of the extrusions. The build surface is also from the original (so it is 1/4" plate vs the 3/8" recommended for the Voron). I've reused two of the Z stepper/leadscrews with a 3rd purchased new for this build. A/B steppers are repurposed from the Hypercube as is the E3D V6 clone hotend. Electronics are all new for this build, with most of the stepper wires reused. I'm running a BTT Octopus v1.1 controller with an EBB SB2209 CAN controller at the StealthBurner. Also using ChaoticLabs aluminum TAP for the Z-Probe... here is a pic of the printer for context:
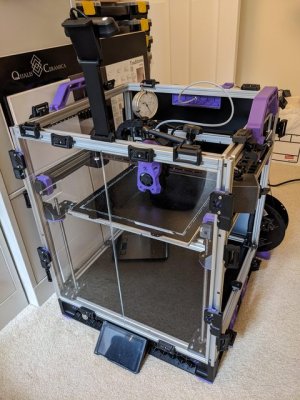
As far as I can tell everything is working well, except for two issues. First, I'm having surprisingly poor first layers. And second, I'm getting a weird effect on the corner of the FilamentCard test print.
So, the first layer problem... After adjusting my Z probe offset (remember, this is a TAP setup) if I try to print my first layer at anything less than 0.3mm layer height I get tearing of the first layer. But at 0.3mm layer height and above I get a very "wobbly" layer. It's almost as if the nozzle is moving up and down as it traverses. Some pics:
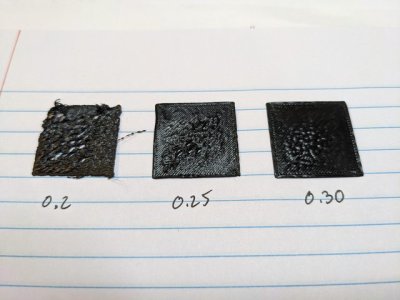
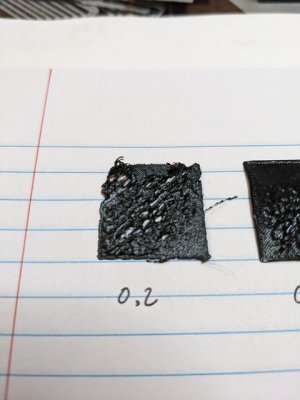
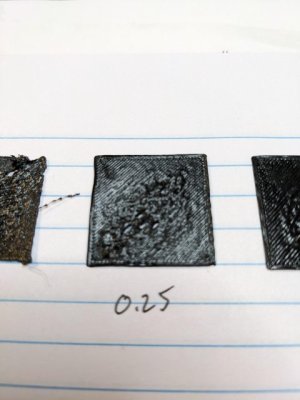
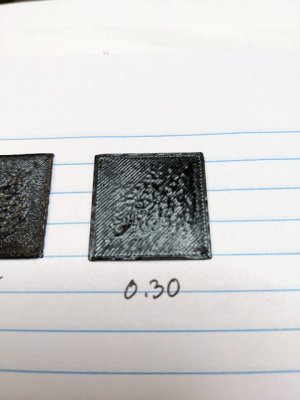
Obviously .2mm and .25mm layer heights are not sticking and the plastic (btw, this is Hatchbox PLA) is lifting/tearing away from the build surface. At .3mm I still seem to be getting some lifting that I assume is causing the waviness you can see in the last image, but it is not being torn away by the nozzle. I'm finding that even at .3mm layer height the lifting/tearing is hit-or-miss.
This is a shot of the edge of the (one layer thick) print. Trying to capture/show the waviness that I seem to be getting.
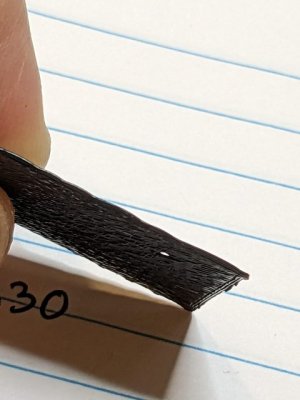
My V2.4 also is using TAP, but I'm using the printed version not the CL version, so I was thinking maybe that was part of the issue? At one point I was wondering if maybe I forgot to add the magnet which holds the print head down when not probing - checked that, the magnet is there. Since it looks to me like the nozzle might be moving up/down while printing I did a test where I homed the Z against a scale, then adjusted Z height down (bringing the build plate up) .005mm at a time recording the nozzle pressure against the scale at each step. If useful I can provide the data, but basically the pressure increased about 10g per .005mm step until it reached about 500g and the Z-probe triggered. After that the pressure remained at about 480g as the nozzle continued "down". That seemed to me like it was working as expected and it would take approx 500g downward force before the print head begins moving upwards, so not likely that the pressure from the filament pushing out the nozzle is causing the head to lift...
I also used a dial indicator in a similar test to see whether the head was actually moving as the bed was brought up in the same .005mm increments. I saw similar results on the scale and the stealthburner head was not lifting until I got close to 500g downward pressure and the TAP broke loose.
Second issue I'm seeing (maybe related?) - when I print the FilamentCard test print I'm getting a strange 'lifting' of the back-right corner:
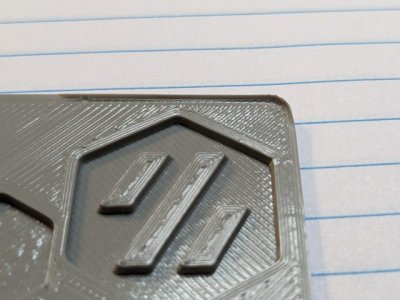
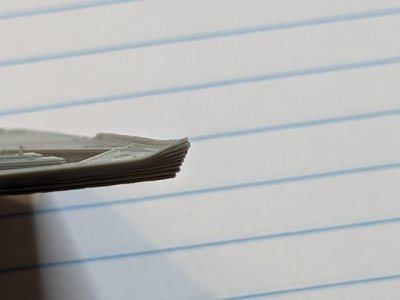
This is consistent across two spools of filament and I've not seen similar artifacts on other test prints:
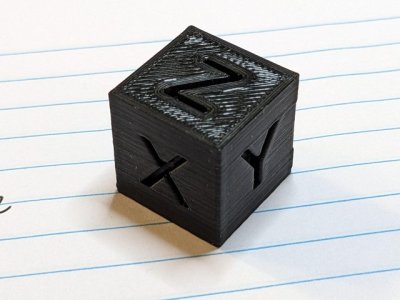
Leading me to assume it has something to do with the way the test card is beveled on that back edge.
BTW, this is the bottom of the test cube:
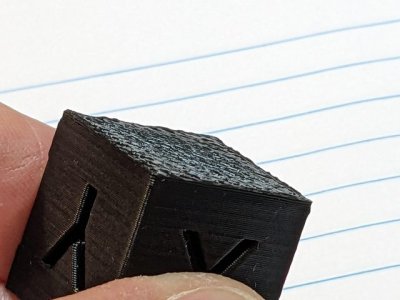
Note how it's wavy and uneven for the first few layers, then seems to settle down and print smoothly for the remaining layers.
I'm out of ideas on what to try for these problems. Any suggestions would be appreciated.
Thanks in advance!
Last edited: