Brawler215
Member
- Printer Model
- Trident
- Extruder Type
- Clockwork 2
- Cooling Type
- Stealthburner
I have recently completed my Trident 300, and it has gone very well except for a very weird issue. I can print out an object like the Voron calibration cube perfectly fine, with everything square and no issues or artifacts. But, once I try to print anything that will introduce higher accelerations, a massive skew gets introduced into the prints in the X direction.
I have been trying to print out a bunch of small fasteners for a project, and every batch has turned out like this: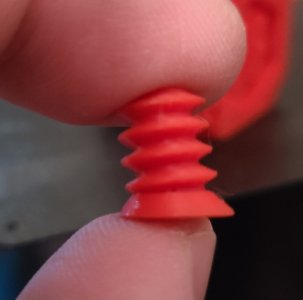
That countersink on the screw head is supposed to be totally symmetrical, but it is obviously very skewed. The Voron calibration cube in the background was printed using the same slicer settings and printer configuration, but it came out totally square.
The only thing that has followed the problem has seemed to be either prints with a bunch of small parts (which then would use a lot of travel moves to zip between parts at max speed) or larger parts which are irregular and have lots of quick direction changes of the toolhead. I am using a max toolhead speed of only 300mm per second, and klipper is limiting accelerations to 3000mm/s^2, so I do not think I am doing anything out of the ordinary.
Does anyone have any ideas? Thanks!!
I have been trying to print out a bunch of small fasteners for a project, and every batch has turned out like this:
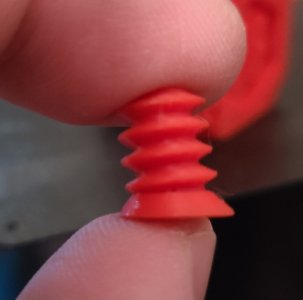
That countersink on the screw head is supposed to be totally symmetrical, but it is obviously very skewed. The Voron calibration cube in the background was printed using the same slicer settings and printer configuration, but it came out totally square.
The only thing that has followed the problem has seemed to be either prints with a bunch of small parts (which then would use a lot of travel moves to zip between parts at max speed) or larger parts which are irregular and have lots of quick direction changes of the toolhead. I am using a max toolhead speed of only 300mm per second, and klipper is limiting accelerations to 3000mm/s^2, so I do not think I am doing anything out of the ordinary.
Does anyone have any ideas? Thanks!!