Durahl
Well-known member
I'm thinking about modding a CPAP Air Supply System into my StealthBurner and have noticed these usually being built with a WS7040 BLDC FAN and matching 24V Controller Board which is all fine and dandy but these Controller Boards seem to come with a 6-Pin Connector exiting two 3-Wire Bundles - One such Bundle leading to a 3-Wire Rotary Dial with the other Bundle either having lose ends to connect to something or being unpopulated.
Does anyone have any sources as to how that system is usually being controlled via the Printers MCU?
Also... Is there a particular reason as to why we need a WS7040 BLDC Fan with such a Controller to begin with instead of using another run of the mill - albeit larger - Radial 24V Fan?
Thanks in advance!
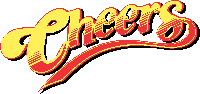
Does anyone have any sources as to how that system is usually being controlled via the Printers MCU?

Also... Is there a particular reason as to why we need a WS7040 BLDC Fan with such a Controller to begin with instead of using another run of the mill - albeit larger - Radial 24V Fan?

Thanks in advance!
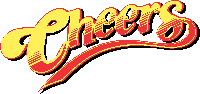