The biggest obstacle to printing speed is that plastic cannot be melted quickly.
Instead of the traditional approach of bringing the nozzle to the desired temperature and continuing to print, the method is to calculate the amount of plastic to be consumed in the next second and give the necessary energy.
In large extrusion systems and filament producers, preheating is done.
The plastic is first heated and melted in the front channel. In the second channel, enough energy is given to increase its fluidity. An induction heater would be great instead of traditional heaters. I want to pass through a graphite or steel channel by heating it with induction.
The maximum flow rate in mass production currently on the market is around 140 mm3/s. This value is very low. You should test the speeds you can imagine.
Currently I can already print at 600mm/s. I already get a smooth output at 600mm/s. I aimed for more. Print speed is 600, not travel speed.
Think big, set a goal and achieve that goal.
CAD files have the STEP extension, so when I open them in Solidworks, 1575 different solid object shapes are created. When I want to access the parts and make changes to them, I cannot change the design as I wish because I have to define each process from scratch. Due to the different approach between Fusion and Solidworks, files saved as sldpart or sldasm are required. I can rebuild the parts myself, but that takes a lot of time.
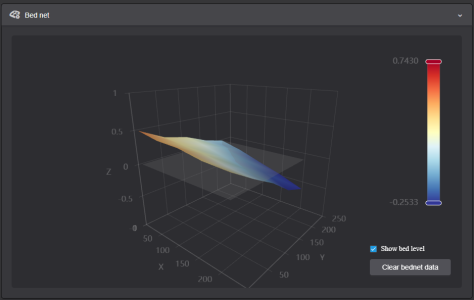
The difference in the picture is a terrible table leveling. This is a easy situation for the Klipper. During printing, the z-axis corrects itself with small movements. I can easily get a piece without any problems.