I recently finished my LDO V2.4 350mm build with the above mentioned LDO supplied bed and heater. I found that when heating the bed it would also make the led strip lights plugged in near the printer flicker. After much internet searching I found that the default PWM frequency for the Klipper config is 50hz. I live in the US and have 60hz power. I updated the PWM to pwm_cycle_time: 0.01666 and that stopped the flickering lights. I've run a few small sub 1 hour prints with PLA so a bed temp of 60C and no issues. I tried to run something with a higher bed temp and I kept getting Klipper crashes stating Heater heater_bed not heating at expected rate. I have increased the check_gain_time up to 100 and it still won't reach full temperature and also crashes trying to run a PID tune. I've attached a screenshot below. The left blue trace is requesting 80C at 60hz and it's all choppy and eventually falls off completely. The middle trace is requesting 100C at 50hz while I had the bed raised checking voltages. I couldn't find any issues so I stopped it and reassembled and started a 100C PID tune.
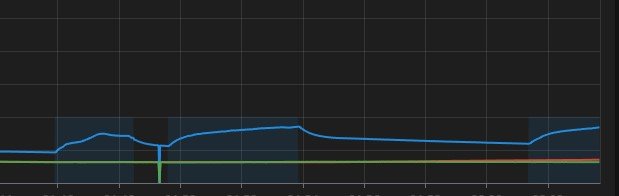
Below is a trace of the completed PID tune at 100C and 50hz.
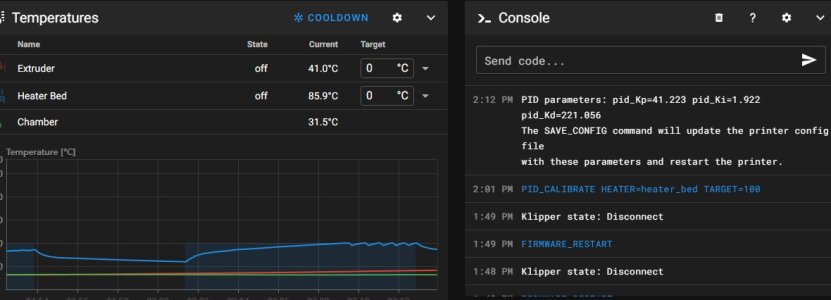
I have my max bed power set to 60% as per the setup guide to not exceed the SSR rating. Is there any reason why I can't set the PWM frequency to 60hz to stop the light flicker? I'm guessing it is switching faster than the SSR can handle as it almost acts like an extruder losing steps as far as the temperature goes. During the entire heat cycle the heater status is solid at 60% until Klipper crashes even though the temperature is swinging quite a bit. As you can see though it is a smooth trace at 50hz.
Similar but different topic. Even after heating for an hour, I have a 10-15C delta compared to the thermistor reading vs the actual flex plate temperature, the flex plate being lower.
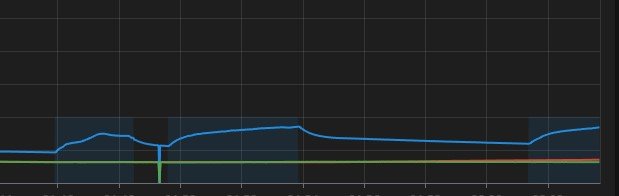
Below is a trace of the completed PID tune at 100C and 50hz.
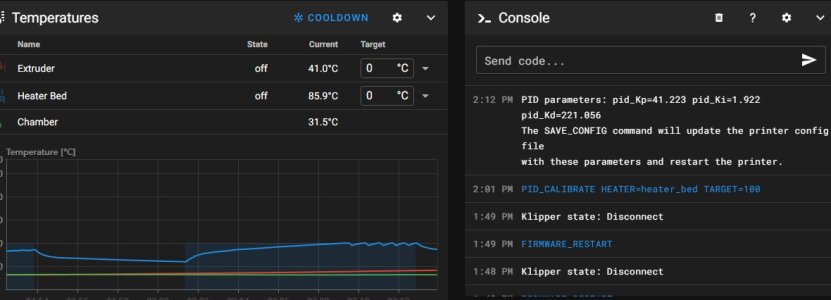
I have my max bed power set to 60% as per the setup guide to not exceed the SSR rating. Is there any reason why I can't set the PWM frequency to 60hz to stop the light flicker? I'm guessing it is switching faster than the SSR can handle as it almost acts like an extruder losing steps as far as the temperature goes. During the entire heat cycle the heater status is solid at 60% until Klipper crashes even though the temperature is swinging quite a bit. As you can see though it is a smooth trace at 50hz.
Similar but different topic. Even after heating for an hour, I have a 10-15C delta compared to the thermistor reading vs the actual flex plate temperature, the flex plate being lower.