OlegMalykin
New member
- Printer Model
- Voron 2.4
- Extruder Type
- Clockwork 2
- Cooling Type
- Stealthburner
Hi
I tried, but I didn’t find a posts on this topic.
Why doesn't anyone assembly Vororn 2.4 without cable chains?
We can do the wiring like a canbus assembly\wiring.
I don't want to connect the canbus, but I'm thinking of assembling the wires as shown in the picture.
What do you think?
Why doesn't anyone do this?
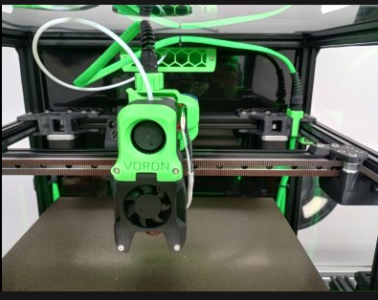
I tried, but I didn’t find a posts on this topic.
Why doesn't anyone assembly Vororn 2.4 without cable chains?
We can do the wiring like a canbus assembly\wiring.
I don't want to connect the canbus, but I'm thinking of assembling the wires as shown in the picture.
What do you think?
Why doesn't anyone do this?
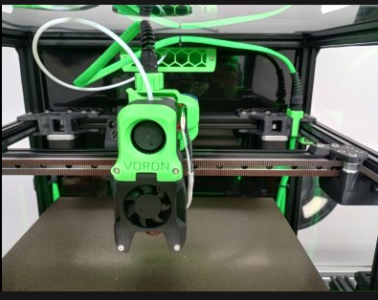