Upperbottom
Active member
I'm about to start building a Voron 2.4 with a Formbot Kit as base (yea NOW I know it's a lottery...but at least the cables come pre-cut and crimped), then add Tap. Stealtburner is now standard in the FB-Kit..
What could possibly go wrong
Currently only the Tap-kit and the Formbot parts have arrived. Eventually I will get my printed parts but while waiting I greased the rails (veeery satisfying work and nice woshwoshwosh), I checked the BOM and I'm currently prepraing myself for an inhumane amount of heatset inserts.
The picture shows my current printer (ReprapPro Mendel Tricolour) printing it's first VoronLogo in the heatset-trainers.. Unsuspecting of it's future in my parts-and-projects drawer...
"You served me well, now it's time to rest"*
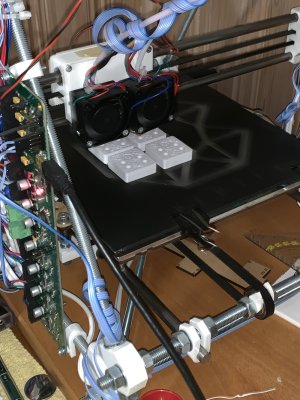
Next up: convincing my better half to yield the kitchen counter for a day to get a great square frame...
*ok.. this sounds much more affectionate than it should be... NO automatisation whatsoever, the cooling is abysmal, speed would probably be better to use a 3d Pen, ringing more than an ancient schoolbell and the killer is a tempramental Z-axis that punishes any sudden and fast moves by seizing up and drooping one side... However: it was my printer, it could in theory print 3 colors and i learned a lot building and maintaining it**
**yes.. I know.. I could probably adress a lot of these issues with tuning, adding better cooling fans, better bed, better Z-axis bearings and screws and maybe a bed probe and new firmware.. maybe klipper? But then again.. why not a new one. Just because you can still drive a t-ford why not build something more modern...
What could possibly go wrong

Currently only the Tap-kit and the Formbot parts have arrived. Eventually I will get my printed parts but while waiting I greased the rails (veeery satisfying work and nice woshwoshwosh), I checked the BOM and I'm currently prepraing myself for an inhumane amount of heatset inserts.
The picture shows my current printer (ReprapPro Mendel Tricolour) printing it's first VoronLogo in the heatset-trainers.. Unsuspecting of it's future in my parts-and-projects drawer...
"You served me well, now it's time to rest"*
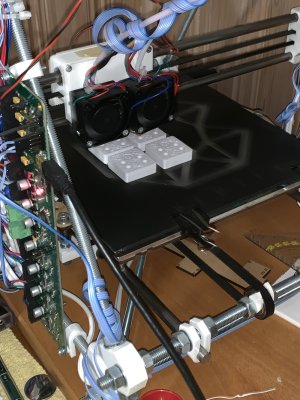
Next up: convincing my better half to yield the kitchen counter for a day to get a great square frame...
*ok.. this sounds much more affectionate than it should be... NO automatisation whatsoever, the cooling is abysmal, speed would probably be better to use a 3d Pen, ringing more than an ancient schoolbell and the killer is a tempramental Z-axis that punishes any sudden and fast moves by seizing up and drooping one side... However: it was my printer, it could in theory print 3 colors and i learned a lot building and maintaining it**
**yes.. I know.. I could probably adress a lot of these issues with tuning, adding better cooling fans, better bed, better Z-axis bearings and screws and maybe a bed probe and new firmware.. maybe klipper? But then again.. why not a new one. Just because you can still drive a t-ford why not build something more modern...