Part 8
I’ve been busy.Busy printing stuff.
Which is awesome, because one big worry I had was if I’d actually use the printer or just end up modding and tweaking it until the end of time.
But of course, I’ve been slowly working through my large mods-I-want list.My initial plan was to write one blog post about modding, but for space and sanity reasons I’ve decided to split it up.
This post goes through a bunch of smaller fixes and mods I’ve done to the printer, and I’ll leave the more involved mods to later posts.
My plan was to take tuning seriously and go through all the tuning guides to get the printer to produce perfect prints. But I didn’t have patience for that and I’ve only made some tweaks when the prints had noticeable defects. Here are the major tweaks I’ve done since the last post:
It got pointed out to me in the
VORON forum that I my right rear Y extrusion was a bit high.The Trident has automatic bed leveling, but because the bed is only attached in three positions it can’t compensate for a difference in the rear that only has a single mount in the middle. If you’re unlucky this might cause issues with bed adhesion.
Turns out I’ve had some problems with bed adhesion. Not a lot mind you, but enough to bother me on some trickier prints.I’ve seen the offset on the corner go down to -0.26, which is more than the standard 0.2 layer height I use, so this might be the cause of some of the issues I’ve seen.
Before adjusting the right Y extrusion.
In the voron_1_trident_questions channel on the VORONDesign Discord there was a pinned message on how to adjust this.I ended up adjusting the front right Y extrusion upwards quite a bit to compensate for this.
After adjusting the front right Y extrusion upwards.
The mesh still isn’t perfect (and it can sometimes look worse than the adjusted picture above), but it’s now a lot better and importantly the rear corners are much more level.
One significant print issue I’ve had is bulging in the corners on overhangs:
Both edges round upwards and apart from being really ugly, they’ve caused a number of prints to fail when the nozzle has knocked loose pieces from the bed or has caused belts to skip.It’s really ugly.
Maybe it was overheating? But it happened consistently, with long layer times, with max fans, and for PLA/ABS/ASA.Another idea was over extrusion, but I think that should’ve shown up in other places?
Then I found the
Bulging section in Ellis’ Print Tuning Guide that made the issue disappear.These were the changes I made:
- Enable external perimiter first
- Set overhang threshold for bridge flow to 0
- I also experimented with disabling overhangs specific settings completely (set bridge speed and fan to 0 or the disable checkbox), but I’m uncertain how effectual that was compared to the other two settings.
Some of these were specific to SuperSlicer, the slicer I use.
These are two prints that show the difference between the settings. The green is without the changes and white is with the changes.Apart from the overhangs, the green printout looks pretty good, but the overhangs look terrible. The white still has some defects, but it’s
so much smoother.
I had printed for around 400 hours when the extruder suddenly started skipping.At first it was just minor artifacts, but after a while prints started failing in major ways or refusing to extrude anything at all:
My first idea was that I had messed up the tension in the extruder, so it no longer got a good grip on the filament. (I had some major issues with loading filament at one time, and I started screwing around with everything I could think of.)
But alas I couldn’t solve it with a quick-fix, so I had to open up the toolhead. Which I should have done much sooner, because there were a bunch of broken filament stuck in the gears:
One piece of broken filament inside the CW2, together with a bunch of dirt.
I really didn’t want to disassemble it because I was afraid of the effort to do so, but in the end it was just a few screws and the whole cleaning process took 10 min. Building your own printer has some benefits, I should have more faith in the process.
There were a lot of leftovers after the build; nuts, screws, belts, etc. But also an unused bag with “Teflon Tubing, 4x2mm”, which surely shouldn’t be completely unused?
Turns out you’re supposed to use a tube with an inner diameter of 2mm between the extruder and hotend, but I had used the regular PTFE tube that had an inner diameter of 3mm. This isn’t ideal and requires more retraction (which I didn’t compensate for), and it can cause stringing issues (which I had).
Note to self: Don’t use a tube with an inner diameter of 2mm between the extruder and spool, the filament will get stuck due to friction.
For a long time I was really happy with how my first layers looked and I could start a print and it would finish without issue most of the time.
But sometimes I had these “blobs” that started collecting:
This is some extra filament that has been pushed around and gotten stuck on the print.
I couldn’t figure out where it was coming from. Overextrusion maybe, but i didn’t find any issues with it and this only happened in the beginning of the print.
And later on I started to get
severe issues with bed adhesion where I felt lucky if a part stuck around long enough for the print to finish.The first layer started to look garbage as well:
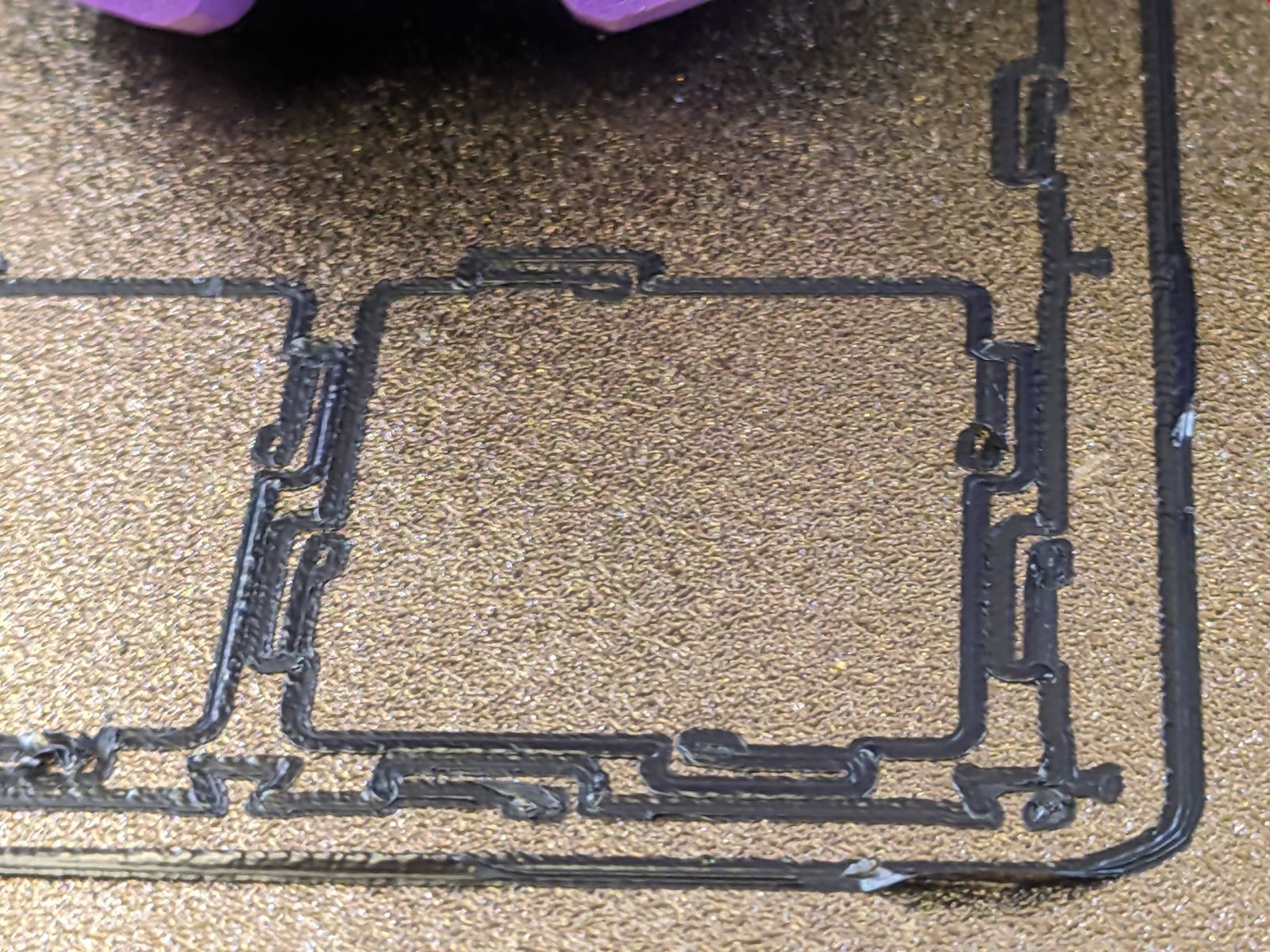
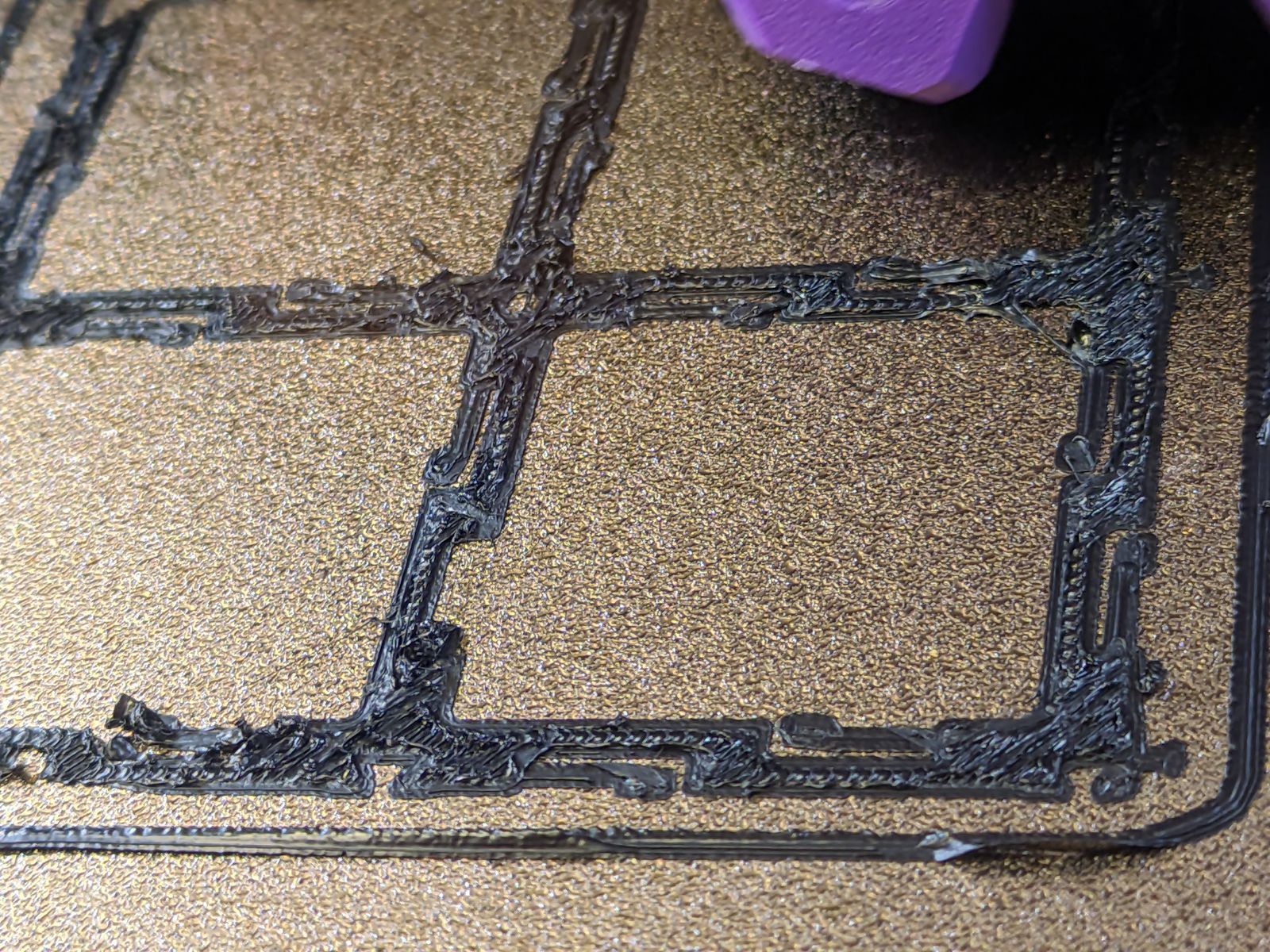
The worst part is, I didn’t think I had changed anything.
In hindsight me fixing the
bed mesh offset might have been the cause my sudden problems.
I tried a bunch of things; changing nozzle, recalibrating PA and EM, changing filament, and even replacing the extruder (more on that in a future post) yet the issue remained.
What finally fixed it was recalibrating the
z offset and tuning
first layer squish once more. I’m not sure why I had to do this again (doesn’t Tap magically solve everything?), but now the first layer is pretty and the bed adhesion problems are almost completely gone. (Some prints have a tendency to warp a little, but I guess it’s hard to get things perfect.)
Much better first layer!