MichaelOToole
Well-known member
General remarks re LDO kit, and ChaoticLab CNC Metal Parts...
Also includes general questions & answers relating to getting printer up and running...
The CL (CharticLab) kit is top notch but quite expensive, even so, every single part was perfect not even a single blemish.
The LDO kit was 99.9 % perfect, only a couple of the pulleys/idlers slug threads were iffy.
If I make another Voron I will choose something less expensive, perhaps the FYSETC version as it's half the price and reviews Iv'e seen are quite good.
The Build:
Main reference: Voron 2.4 CNC parts Kit Build Guide (here) as my main reference, switching to the LDO Voron Build Guide for a cross reference.
As far as I can tell at this stage*, I only need to print cosmetic parts such as the skirting thingy to complete the project.
Some parts will be duplicated for example you will end up with a few spare bearings and lots of nuts and bolts.
One minor issue was a reference to M3x28 bolt sizes in the CL box, it was actually M3x27 (1mm smaller that referenced)...
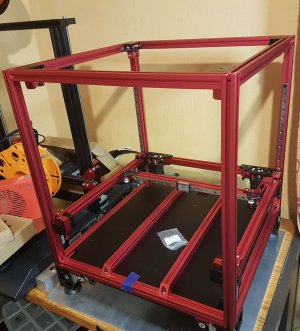
That's all for now, will keep track of next section and post anything of interest, I Just wanted to mention the quality of both kits is excellent, if a little pricey ...
* please check later posts for updates...
Notes: 22 March 2024
Check the top aluminium part (blue in image below) that locks the Z belts in place, make sure these are horizontal (parallel to the bottom part and not at an angle).
On my build, the M5x16mm screws were a bit too long, bottoming out before fully securing the belt leaving them angled, the front belts slipped.
As I didn't have shorter bolts, I added a 1.5mm washers for each... that did the trick...
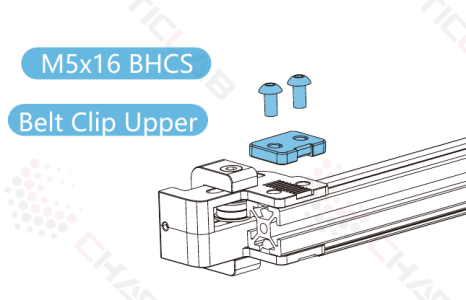
Notes: 23 March 2024
In software you will/may need to flip the 4.3" TFT Display
1: Open config.txt file on SD card...
2: Find and Comment out dtoverlay=vc4-fkms-v3d, if not already done... add a # at start of line
3: Add these lines to end of file:
display_lcd_rotate=2
dtoverlay=rpi-ft5406,touchscreen-inverted-x=1,touchscreen-inverted-y=1
4: Replace SD card and test, the display should now be correct...
Reference Doc here...
Also includes general questions & answers relating to getting printer up and running...
The CL (CharticLab) kit is top notch but quite expensive, even so, every single part was perfect not even a single blemish.
The LDO kit was 99.9 % perfect, only a couple of the pulleys/idlers slug threads were iffy.
If I make another Voron I will choose something less expensive, perhaps the FYSETC version as it's half the price and reviews Iv'e seen are quite good.
The Build:
Main reference: Voron 2.4 CNC parts Kit Build Guide (here) as my main reference, switching to the LDO Voron Build Guide for a cross reference.
As far as I can tell at this stage*, I only need to print cosmetic parts such as the skirting thingy to complete the project.
Some parts will be duplicated for example you will end up with a few spare bearings and lots of nuts and bolts.
One minor issue was a reference to M3x28 bolt sizes in the CL box, it was actually M3x27 (1mm smaller that referenced)...
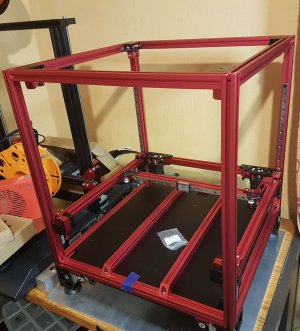
That's all for now, will keep track of next section and post anything of interest, I Just wanted to mention the quality of both kits is excellent, if a little pricey ...
* please check later posts for updates...
Notes: 22 March 2024
Check the top aluminium part (blue in image below) that locks the Z belts in place, make sure these are horizontal (parallel to the bottom part and not at an angle).
On my build, the M5x16mm screws were a bit too long, bottoming out before fully securing the belt leaving them angled, the front belts slipped.
As I didn't have shorter bolts, I added a 1.5mm washers for each... that did the trick...
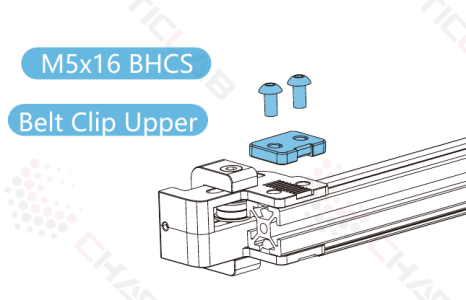
Notes: 23 March 2024
In software you will/may need to flip the 4.3" TFT Display
1: Open config.txt file on SD card...
2: Find and Comment out dtoverlay=vc4-fkms-v3d, if not already done... add a # at start of line
3: Add these lines to end of file:
display_lcd_rotate=2
dtoverlay=rpi-ft5406,touchscreen-inverted-x=1,touchscreen-inverted-y=1
4: Replace SD card and test, the display should now be correct...
Reference Doc here...
Attachments
Last edited: