MichaelOToole
Well-known member
Here we go...
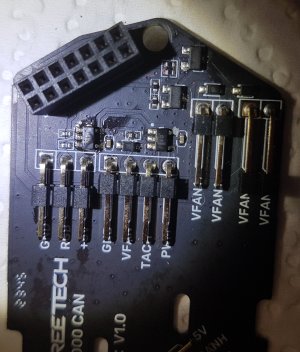
Blistered IC...
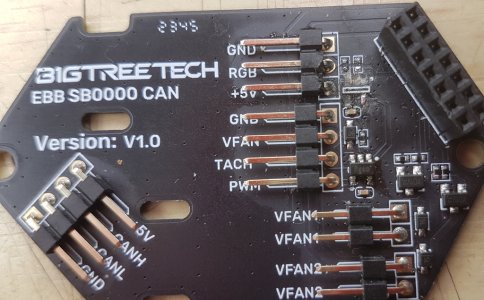
Component fell off this one, it was not damaged or marked, the damage is from my poor attempt to re-seat the component with poor eyesight and no optics.
I do have the necessary equipment (trinocular microscope) but no room to set it up and I am a pretty good solderer after 45 years of doing it...
Again in hindsight, I should have tested the component before re-soldering it, it was probably faulty by then...
I've ordered 10 replacement buffers, best get out my microscope, it hasn't had any work this year...
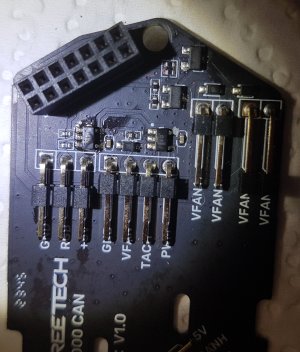
Blistered IC...
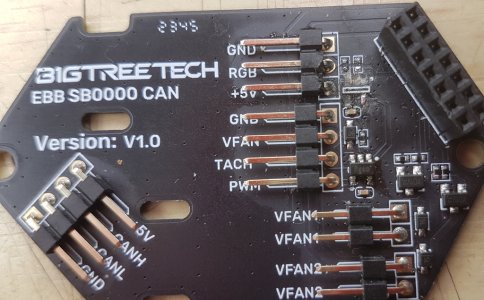
Component fell off this one, it was not damaged or marked, the damage is from my poor attempt to re-seat the component with poor eyesight and no optics.
I do have the necessary equipment (trinocular microscope) but no room to set it up and I am a pretty good solderer after 45 years of doing it...
Again in hindsight, I should have tested the component before re-soldering it, it was probably faulty by then...
I've ordered 10 replacement buffers, best get out my microscope, it hasn't had any work this year...

Last edited: