The Machine
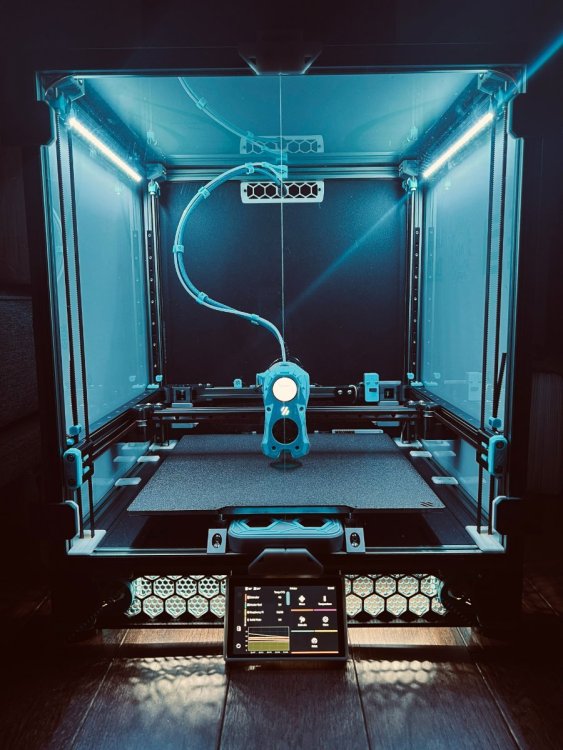
Background / The Kit:
Having finished my first Voron (build log here), it seems I have caught the bug! The main goal of that printer was to use the 0.2r1 to print all parts for a 2.4r2. The main goal of this printer is to aim for Serial #7000!
I researched for a few days, self-source vs kits and decided that a kit would be the best value for my own needs. Even adding on the options I wanted to a kit was cheaper than self-source for me. Although I really loved my Formbot 0.2r1 kit, I settled with a fully comprehensive kit from Magic Phoenix (MPX) as it ticked a few more boxes 1) Canbus and TAP included - plus all the boards and hardware, 2) Cheaper - living in a post-Brexit UK meant a huge bill for import tax. MPX had an option of slow shipping with taxes included. 3) Support - before I bought the kit, I was in regular contact with the owner on the official Voron Discord and their Discord to make sure my needs were met. I already had a 120mm V0.2, a 225mm CR6-SE so 350mm was the right size for me.
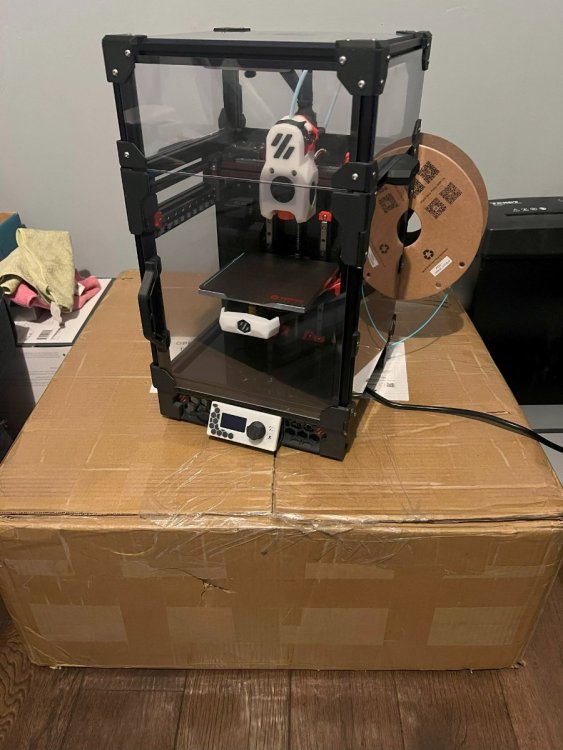
[V0.2r1 on top of shipping box]
Additional items I bought:
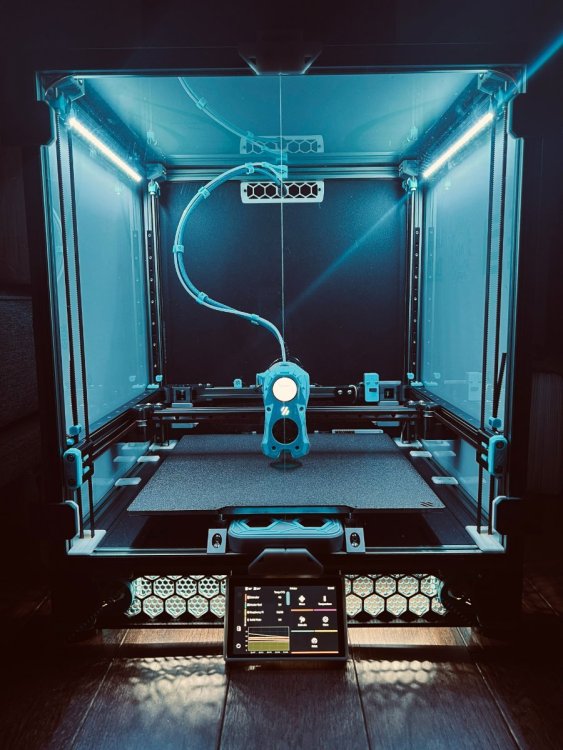
Background / The Kit:
Having finished my first Voron (build log here), it seems I have caught the bug! The main goal of that printer was to use the 0.2r1 to print all parts for a 2.4r2. The main goal of this printer is to aim for Serial #7000!
I researched for a few days, self-source vs kits and decided that a kit would be the best value for my own needs. Even adding on the options I wanted to a kit was cheaper than self-source for me. Although I really loved my Formbot 0.2r1 kit, I settled with a fully comprehensive kit from Magic Phoenix (MPX) as it ticked a few more boxes 1) Canbus and TAP included - plus all the boards and hardware, 2) Cheaper - living in a post-Brexit UK meant a huge bill for import tax. MPX had an option of slow shipping with taxes included. 3) Support - before I bought the kit, I was in regular contact with the owner on the official Voron Discord and their Discord to make sure my needs were met. I already had a 120mm V0.2, a 225mm CR6-SE so 350mm was the right size for me.
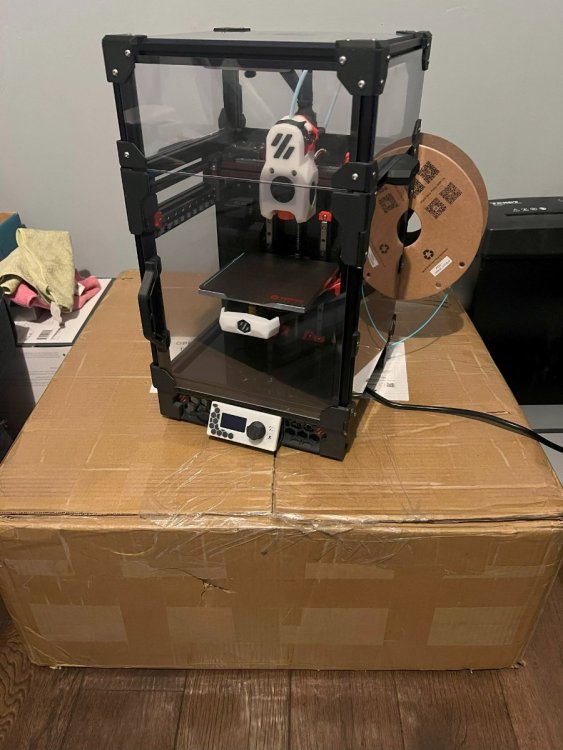
[V0.2r1 on top of shipping box]
Additional items I bought:
- Galileo 2 kit from OneTwo3d
- Hardware for THE FILTER
- Hartk hardware - Pins mod and GE5C bearings
- Stainless Steel MGN12 with medium pre-load
- BTT Octopus Pro (Whilst the MPX kit contains M8Pv2+CB1, I wanted to have separate MCU and RPI 3b+ for better hardware / software support)
- BTT PI TFT50
- BTT KNOMI 2
- Meanwell PSU RS-25-5 (To power the RPI)
- CNC Metal Tap (Vitalli design)
- Rainbow BARF LEDs
- Klipper Expander
- Aukey PC-LM1E USB webcam
- Stainless Steel MGN12 linear rail with medium pre-load
Last edited: