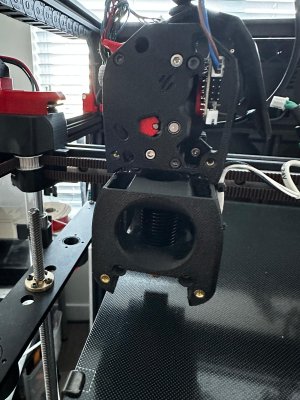
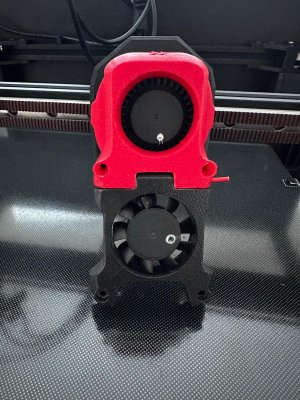
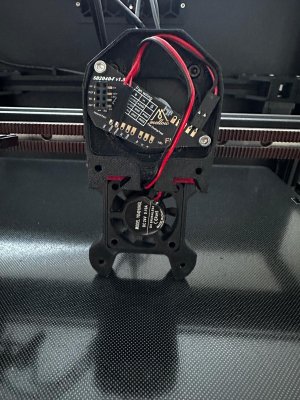
This is a bit of an unholy hybrid of a few things
1. SB's CW2 extruder
2. The Mellow SB2040 split toolhead CANBUS PCB
3. The 5015 Fan Mod for the AB (https://github.com/Greg191134/Voron/tree/master/Afterburner Optimisation/5015 fan mod)
I used the 5015 mod well for two reasons, extra airflow (and parity with the SB part cooling fan) .. but also its shape is larger, it fits more neatly on top of the SB extruder.
I modded the back piece of this mod to basically hollow it out to add space to fit the split PCB and sink the screws holding the front half deeper for the same reason. I also added some pins to the PCB (had to source thinner ones than the standard ones) to be able to disconnect the fans easily, especially the bottom one, since AB kind of relies on this idea.
I suppose I could go through a few more revisions there and move the screws from the back to the front, it just didn't really seem worth it, given that for the bottom right pcb screw I still would be stuck with ~3mm of space ..
Although now that I write this .. I do have some M2 heat inserts from another project .. those are only 3mm deep .. I forget if I have 2mm or 3mm to work with there .. if its 3 .. it would be way more secure with those smaller screws, but into a heat insert .. and then it may be worth moving the front mounting screws to the front .. to make a bit more horizontal room to fit the insert on the top left side .. dunno .. it works for now .. I can play with in in CAN when the printer is built ..
I feel like out of this project I really should spin out a pile of "little" mods .. kind of separate from this conversion as a whole .. there may be use for them existing a bit more separately ..
The only thing that was particularly annoying about this is that it ended up with a massive overhang (the whole hollow is an overhang) .. so that doesn't look pretty .. but its on the inside .. so who cares

Also the tolerances there are super tight .. the holes for mounting the PCB are super tight and shallow .. One is right beside one of the front holding screws, and literally only has about 3/4 of its diameter actually has plastic, the rest of the screw head opening for the other screw .. the other screw has a full diameter, but its super shallow, since it backs onto the back of the fan housing, so there is literally 3mm to work with there.
I had some M3x3 and M3x4 screws I ended up using there .. it definitely doesn't feel super safe to try remove that PCB more than a couple of times before those holes would probably get stripped.
Ignore the sticking out wires on the first image, I'm not done shortening/crimping all the toolhead things

Another side note ..
I could not come up with a good way to run an X chain .. because of the inverted XY mechanism, there wasn't clearence for the chain loop to properly clear when the toolhead was on max chain extension .. so this build is an umbilical hybrid ..
I still kept a Y chain, it only has the XY endstop cable in it. And the CANBUS wire is going to be pinned to the bowden tube.
I ended up with two custom bits of fittings ..
1. a custom mount for the relief sleeve thing on the back of the CW2 .. its also a bit extra weird because of he inverted nature of the whole setup, the spot where the magnet for the X endstop had to move from the X rail mount itself, to the little arm on the back of the CW2 (which was very convenient, this is a super easy piece to swap out and iterate on, I'd hate to have to swap out the stuff holding the belt in place and have to re-square the XY and re-tension the belts each time

2. a custom little cube that fits another one of those relief sleeves on the back of the printer .. I figured why not, let's give that a bit of spring as well ..
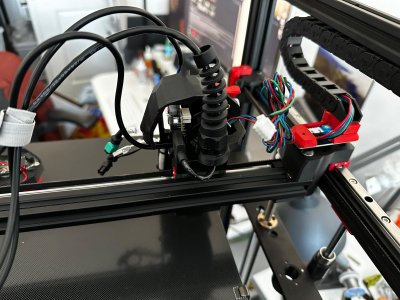
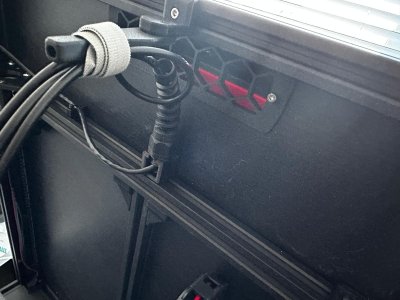
Oh yea .. some notes on build volume ..
Z is looking like I may be able to get about 300mm
X I can just go outside the build plate on either side .. so a full 330mm
Y is not too bad either .. losing ~25mm at the front, and ~5mm on the back .. so still a solid 300mm
So all in all, considering that Voron puts all the components INSIDE the frame .. (Tronxy had pulleys and whatnot on the TOP of the frame, on the CORNERS, so that would have saved a lot of space) .. getting 300x330x300 doesn't seem that bad

---
I look forward to converting this further into a Trident .. right now its almost a working 1.8 style printer

With Trident I can un-invert the XY drive and basically use stock Trident parts there .. the Y chain can switch to being normal Trident style as well.
Given that at its lowest point the bed surface is ~60mm from the deck .. the Trident Z setup should actually be much more compact there and probably get me another 30mm of Z volume maybe ..
I don't think there is much I can do about the X or Y volumes .. unless I can hack the tensioners somehow to be smaller .. they eat ~30mm into the Y .. but this frame uses a 4020 extrusion there .. perhaps if I can mount the tensioner agains that somehow .. it just feels like it'd be harder to make sure its actually square with the axis .. so maybe not .. but there is a lot of potential room on the back .. so perhaps if I can change how the AB mounts work .. I can pretty safely chop out at least 15mm there .. so maybe .. maybe with some more modding I can actualy get back the full 330x330 build volume ..
But first .. get it to fully work .. try to reclaim scraps of build volume later
