Parts finally arrived for the next step.
Gantry - Monolith 2wd 9mm belts
Steppers - steppersonline 17hs19-2504s-h-v1 2.5amp
Pulleys - genuine Gates
Bearings - West3d berzerker flanged 695
Belts - Gates G2 EPDM 9mm
Belting monolith was actually really easy, I remember having some issues the first time i did my other trident but this was really easy.
This took some time to complete, there is no manual or setup guide just a configuration generator and a bom the rest is on you.
If you do decide to ever go down this path which I strongly suggest you do if your looking for the best perfomance upgrade available, its just better, stronger , faster, and the way it should be done, make sure you have fusion so you can view the cad, its how you figure out what goes where.
Once you figure it out its actually fairly simple but at first it got pretty overwhelming but as with all these kind of things make sure your printed parts are as good as you can do, the fitment is everything and will either go swimmingly or bite you in the ass down the road.
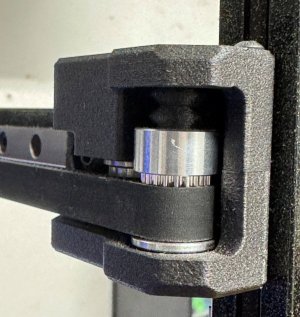
Parts for monolith need to be incredibly strong due to the extreme belt tension so again i used the pccf with 12 walls and 12 top and bottom , sure i could have gone even more exotic with my platic and even gone as far a annealing but I think this will live long enough to be replaced with the cnc version, fingers crossed.
I spent a good amount of time making sure the filament was tuned perfectly or as good as i could anyway so that my tolerances were spot on. I also decided to go 2wd instead of AWD for now , im in pretty much over my head on this build and dealing with AWD just seemed to be to much but I do plan on upgrading as soon as wayne releases the cnc kits for monolith.
After getting this installed I realized I had made a tactical mistake and purchased generic 695 flanged bearings because the good ones were out of stock and I didnt want to wait, I should have waited , as soon as it was belted and i pushed it around manually I had a bad feeling, I also had no idea what to expect nor how a gantry feels at 205hz on the belts so I started asking newbie questions in the discord and as usual left feeling like I still had no idea what to do.
For now it will stay, I have to finish wiring , leds, and some other bits and bobs along with the most frustrating part, the cfg.
Part of the reason I went the easy route and left the 48v and awd to the side is that I have a working cfg on my other trident, same drivers, same type of board only this ones a pro but thats easy enough to figure out so getting up and running shouldnt be to difficult.