Hi All,
Building a Voron Trident or any Voron for that matter in India. Its not as easy as placing an order for a kit and you get a box full of components delivered at your door step with everything nicely labelled and you just have to assemble it. We do not have ready availability of kit in India as of Feb 2024 while I am writing this.
Yes we can import one but the money I would be paying as import duties can be equal to getting another voron printer for that same amount. So, self sourcing is the only option.
I have been extensively planning and gradually buying hardware for my Trident 300 build and I wanted to document each and every nuances, decisions and thought process I took for my build so that if any one else decided to build one he/she can have a reference.
With that I will start by sharing everything related to my build here.
This will be an extremely detailed log . . . .
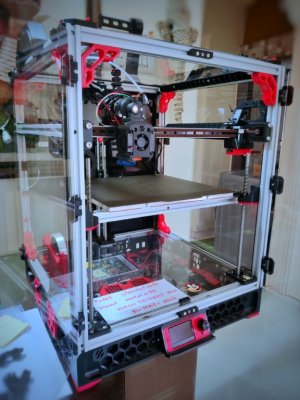

VT.1642
Legend
If this guide helps you build your Voron Trident and would like to support my work.
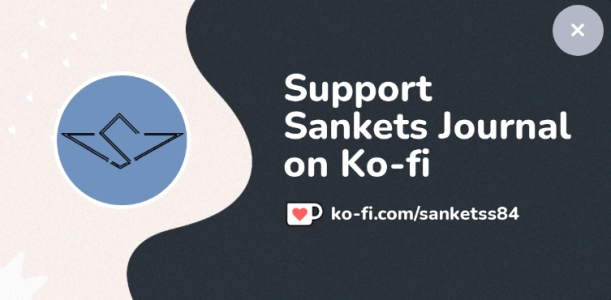
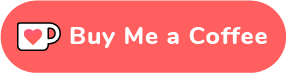
Building a Voron Trident or any Voron for that matter in India. Its not as easy as placing an order for a kit and you get a box full of components delivered at your door step with everything nicely labelled and you just have to assemble it. We do not have ready availability of kit in India as of Feb 2024 while I am writing this.
Yes we can import one but the money I would be paying as import duties can be equal to getting another voron printer for that same amount. So, self sourcing is the only option.
I have been extensively planning and gradually buying hardware for my Trident 300 build and I wanted to document each and every nuances, decisions and thought process I took for my build so that if any one else decided to build one he/she can have a reference.
With that I will start by sharing everything related to my build here.
This will be an extremely detailed log . . . .
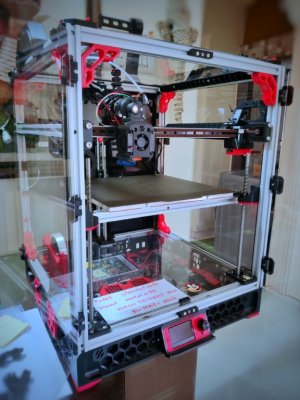

VT.1642
Legend
documented
pending documentation, completed at my end
pending
Why am I building a voron and how did I came up on this decision ? link
Am I aware of other open source 3d printer projects ? link
Which Voron ? link
Why I felt strongly about Voron Trident ? link
What size Trident am I building and Why ? link
Planning Phase link
The Blue Print, The Tool Head and Voron Mods link
Part Selection : The Frame link
Part Selection : Linear Rails link
Part Selection : Nema 17 Stepper Motors link
Part Selection : Power Supply link
Part Selection : Controller Board link
Part Selection : Stepper Motor Drivers link
Part Selection : Bed , Heater and Build Plate link
Part Selection : Can Bus Adapter + Tool Head Can Bus PCB link
Part Selection : Various Wires and Connectors link
Part Selection : Build Tools link
Part Selection : Lubricants link
Part Selection : Tapes link
Part Selection : Extruder, Hotend, Fans, Toohead PCB and Tool head design link
Print voron trident build parts myself or PIF ? link
Why did I decided to print parts myself and challenges faced ? link
The Build : Frame
The Build : AB Drive and Idlers
The Build : Y Axis
The Build : Z Axis
The Build : X Axis
The Build : Belts
The Build : Toolhead
The Build : Wiring Prep
The Build : Electronics
The Build : Controller Prep
pi setup with mainsail os
compile klipper for controller board
can bus setup for toolhead
printer.cfg
The Build : Wiring
The Build : Skirts
The Build : Print Bed (doing this at the very end )
Pre Power Up checks (nero3d)
Ellis print tuning
Setting up slicer for PLA
Testing PLA for few days without panels installed
Setting up slicer for ABS
Testing ABS for few days with panels installed
- Beefy Idlers
- Dragon Burner
- Orbiter V2 extruder mount
- Phaetus Dragon Standard Hotend mount
- Bambulab V2 Hotend mount (alt hotend)
- Klicky Probe mount
- Beacon Mount (alt bed mesh probe)
- Klicky Probe
- The Filter (singles)
- Annex Engineering Panel Clips
- Top Mounted Spool Holder
- Led Bar Clip
If this guide helps you build your Voron Trident and would like to support my work.
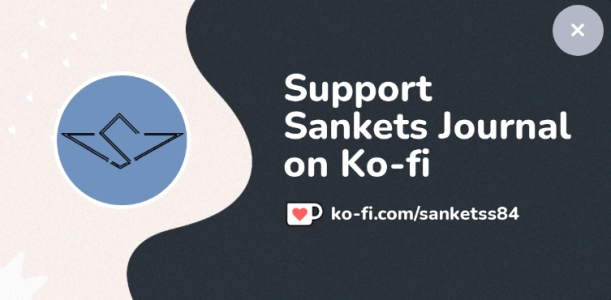
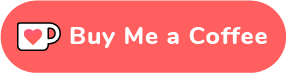
Last edited: