The voron manual/docs mentions the requirements and print settings for 3d printing parts for a voron build.
Print voron trident build parts myself or PIF ?
Voron India discord has quite a few people who can help you print your voron build parts for you and thats a great option to have as not everyone might have a printer that prints abs or just abs per say.
Printing ABS filament is not like printing PLA which is much easier. What you need is a 3d printer which can
- print at 240 to 260 C nozzle temperature
- bed which can support temperature upto 110 C
- heated chamber which can do at least 40C but some might need ~ 50C
- add to that a good exhast system which can route the fumes it produces outside as it can cause headaches and are not the best to inhale directly thats why many people use some kind of filter before they exhaust out the chamber fumes.
Hence for some PIF or Print It Forward program might be a better choice for some who does not want this hassle in their home.
Why did I decided to print parts myself and challenges faced ?
why pif is not best approach for me
- do not need all the parts on trident build
- no control to fine tune the print quality for much better quality
- do not get to rapidly prototype new ideas and mods should I need them
- Wait for the shipment to reach you which can be easily two to 4 days just in shipping and the amount of time the person takes to actually print your parts
So I decided to print the parts on my Ender 3 S1 Pro in a make shift cardboard chamber and used Fibreel ABS filament as my first filament of choice. I did not go with esun ABS as I heard mixed opinions on voron discord so decided to skip it.
This is my make shift chamber , I drop a yoga mat in the front as well to seal the front half. Use a camera hooked into octo print to monitor this remotely.
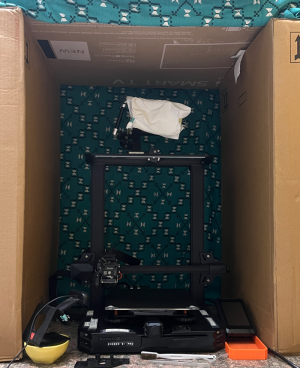
I also use a temperature sensor to monitor my chamber temps for ABS printing
picked this from robu https://robu.in/product/lcd-electronic-fish-tank-water-detector-thermometer/
its battery operated and worked really well.

Voron India discord has quite a few people who can help you print your voron build parts for you and thats a great option to have as not everyone might have a printer that prints abs or just abs per say.
Printing ABS filament is not like printing PLA which is much easier. What you need is a 3d printer which can
- print at 240 to 260 C nozzle temperature
- bed which can support temperature upto 110 C
- heated chamber which can do at least 40C but some might need ~ 50C
- add to that a good exhast system which can route the fumes it produces outside as it can cause headaches and are not the best to inhale directly thats why many people use some kind of filter before they exhaust out the chamber fumes.
Hence for some PIF or Print It Forward program might be a better choice for some who does not want this hassle in their home.

why pif is not best approach for me
- do not need all the parts on trident build
- no control to fine tune the print quality for much better quality
- do not get to rapidly prototype new ideas and mods should I need them
- Wait for the shipment to reach you which can be easily two to 4 days just in shipping and the amount of time the person takes to actually print your parts
So I decided to print the parts on my Ender 3 S1 Pro in a make shift cardboard chamber and used Fibreel ABS filament as my first filament of choice. I did not go with esun ABS as I heard mixed opinions on voron discord so decided to skip it.
This is my make shift chamber , I drop a yoga mat in the front as well to seal the front half. Use a camera hooked into octo print to monitor this remotely.
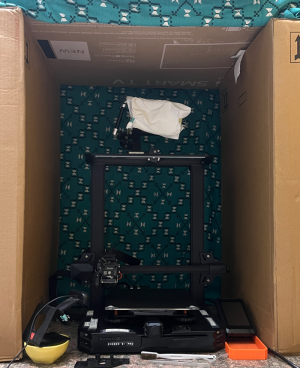
I also use a temperature sensor to monitor my chamber temps for ABS printing
picked this from robu https://robu.in/product/lcd-electronic-fish-tank-water-detector-thermometer/
its battery operated and worked really well.